Carbon Neutrality Pledge
The Altemira Group
aims to achieve carbon neutrality by 2050.
The Altemira Group, through equipment efficiency, use of renewable energy,
and maximization of synergies within the group,
will aim to achieve net-zero Scope 1 and Scope 2 greenhouse gas (GHG) emissions by 2050.
In addition, throughout the group, we will work together to promote initiatives including weight reductions and better recycling rates as we aim to minimize Scope 3 greenhouse gas emissions.
Scope 1: Emissions released from a company's own fuel combustion or production processes (direct emissions)
Scope 2: Emissions from the use of electricity, heat, or steam supplied by other companies (indirect emissions)
Scope 3: Emissions from procurement of raw materials, logistics, disposal, and other means related to the company's activities (indirect emissions other than Scope 1 and 2)
GHG :Green House Gas
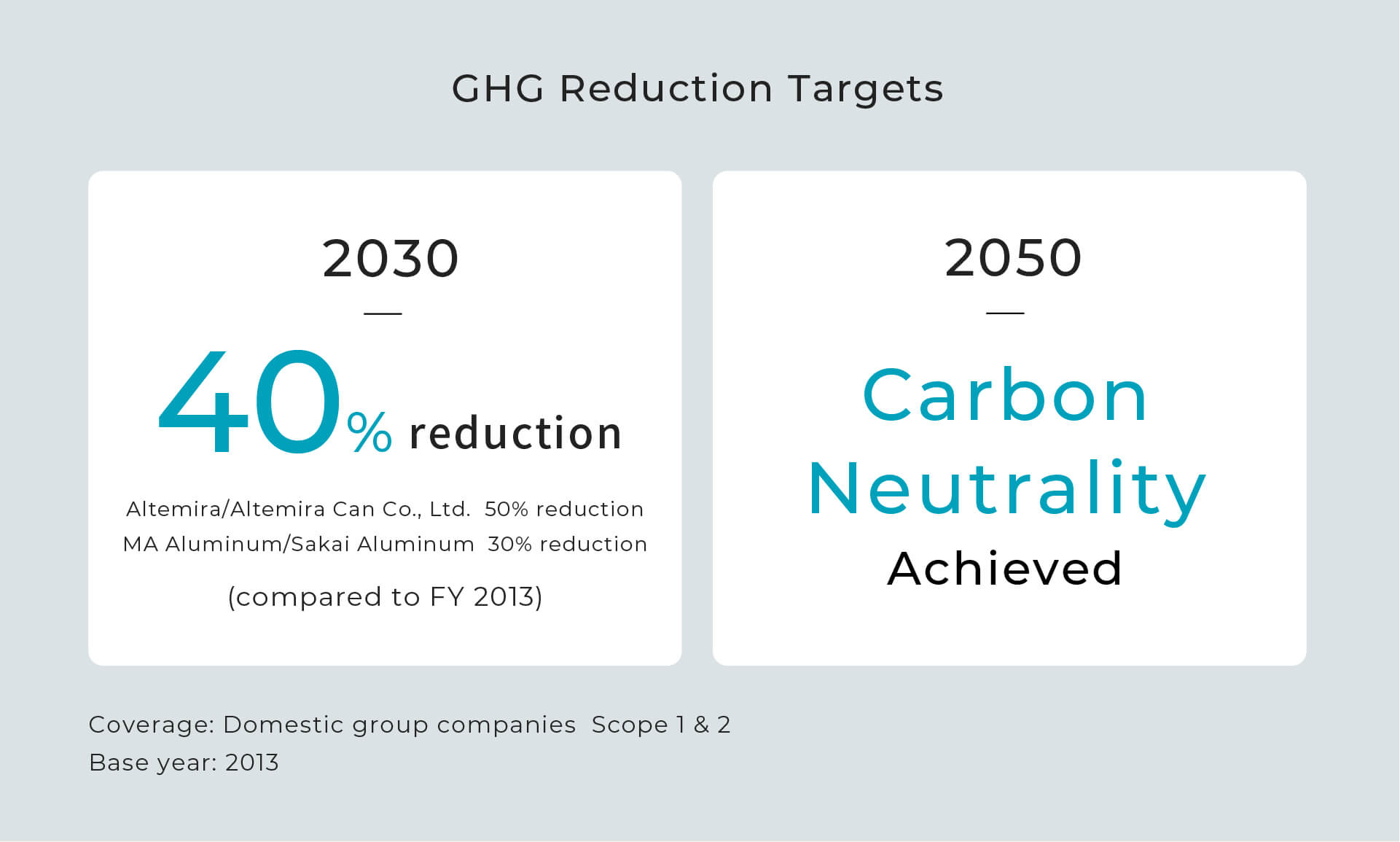
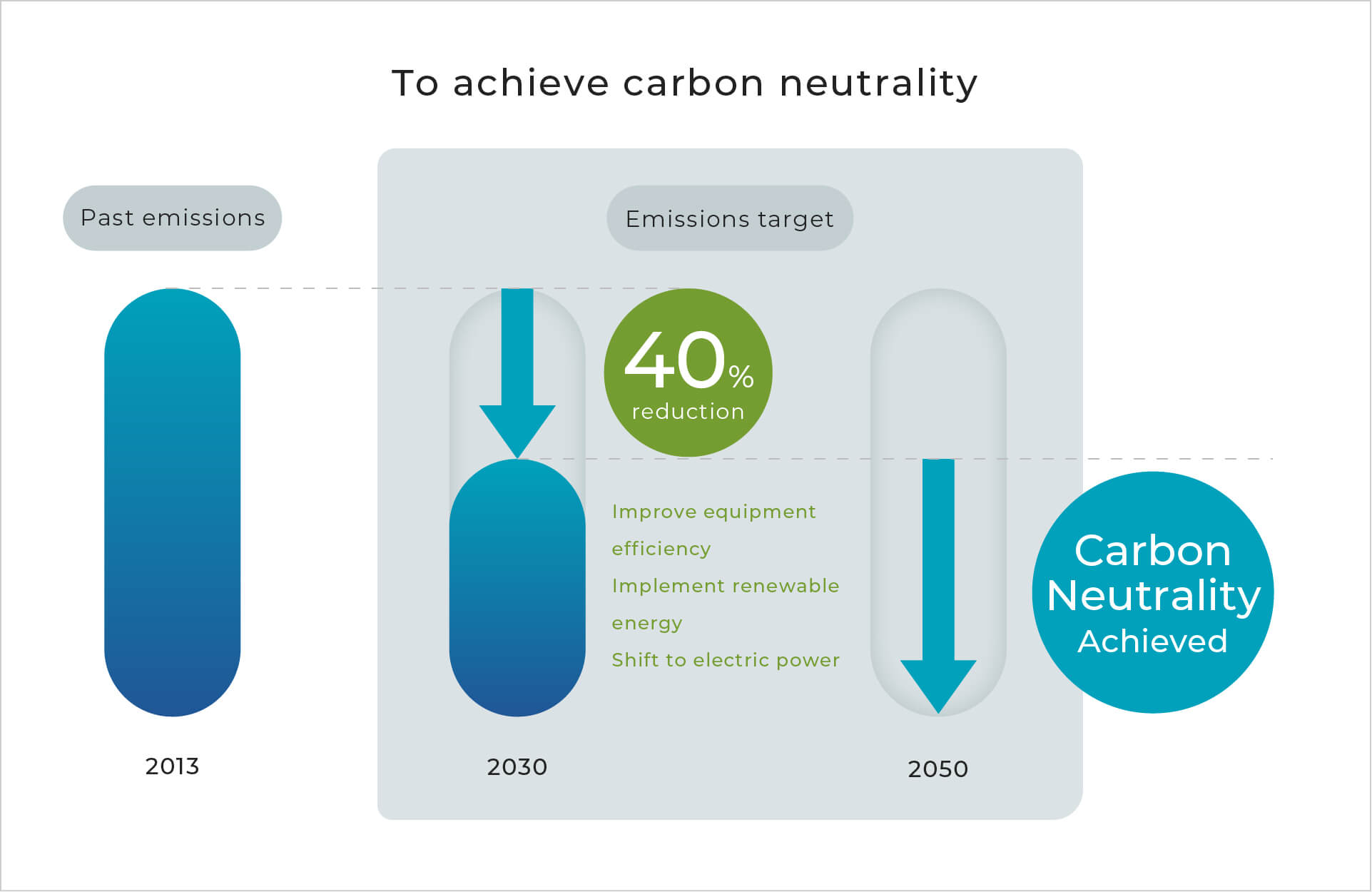
Equipment Efficiency / Change in Fuel Type
Cut GHG Emissions by upgrading our homogenizing furnace* (and changing the type of fuel used)
We implemented the steps below in our casting process to significantly reduce our greenhouse gas emissions.
- Upgrades to the homogenizing furnace improve insulation and heat circulation efficiency within the furnaces
- Changed the fuel type from kerosene to natural gas
*The homogenizing furnace is a piece of equipment used for heat-treating the aluminum and correcting non-uniform metallic grain structure after the casting process.

Equipment Efficiency / Waste Heat Recovery
Conserving Energy by Introducing Waste Heat Recovery Unit
The machine for washing aluminum features a drying tank for drying the solvent on the aluminum surface. Installing a waste heat recovery unit in this equipment has enabled energy saving through reuse of heat discharged from the drying tank.
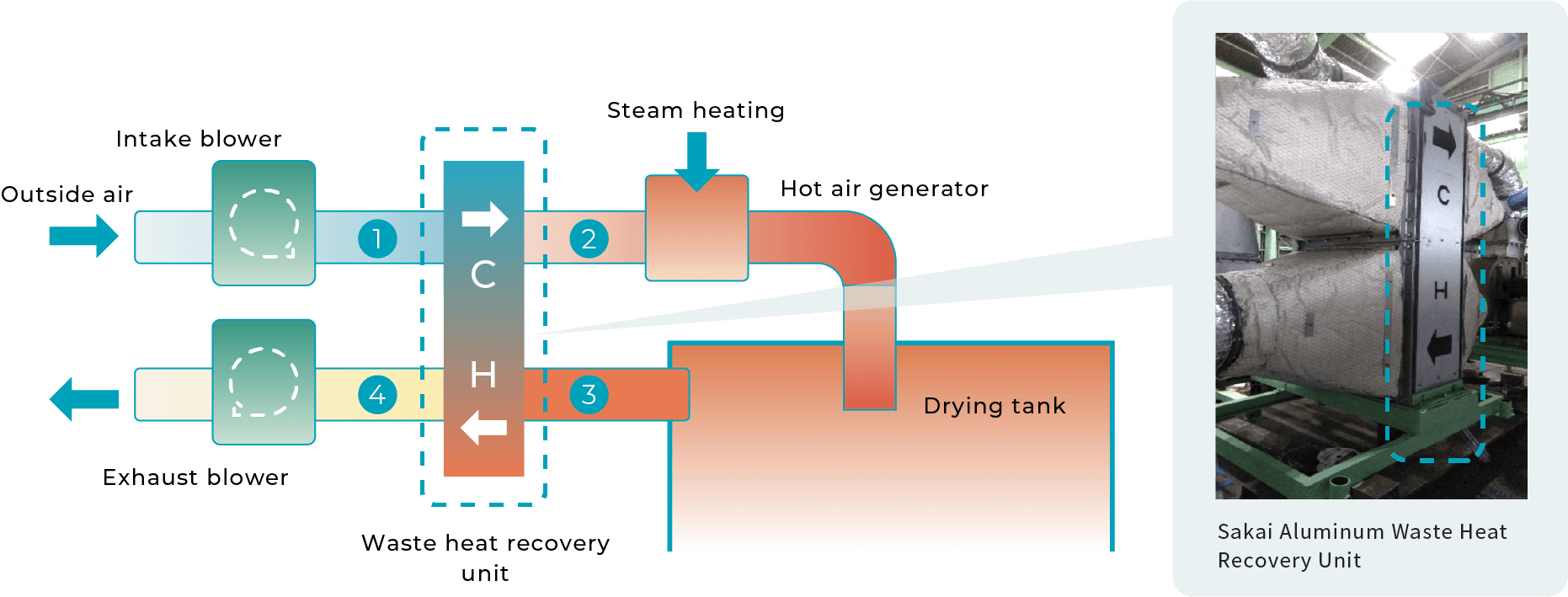
Equipment Efficiency / Energy Loss Reduction
Conserving Energy in the Paint Drying Process
The inside coating of aluminum cans is dried during manufacturing, a process that uses heat from gas combustion. We implemented the steps below to minimize energy loss and reduce greenhouse gas emissions.
- Changing the conveyor net for the oven used for drying to a resin material with lower thermal conductivity.
- Applying heat-shielding paint to the side walls of the oven for heat dissipation reduction.
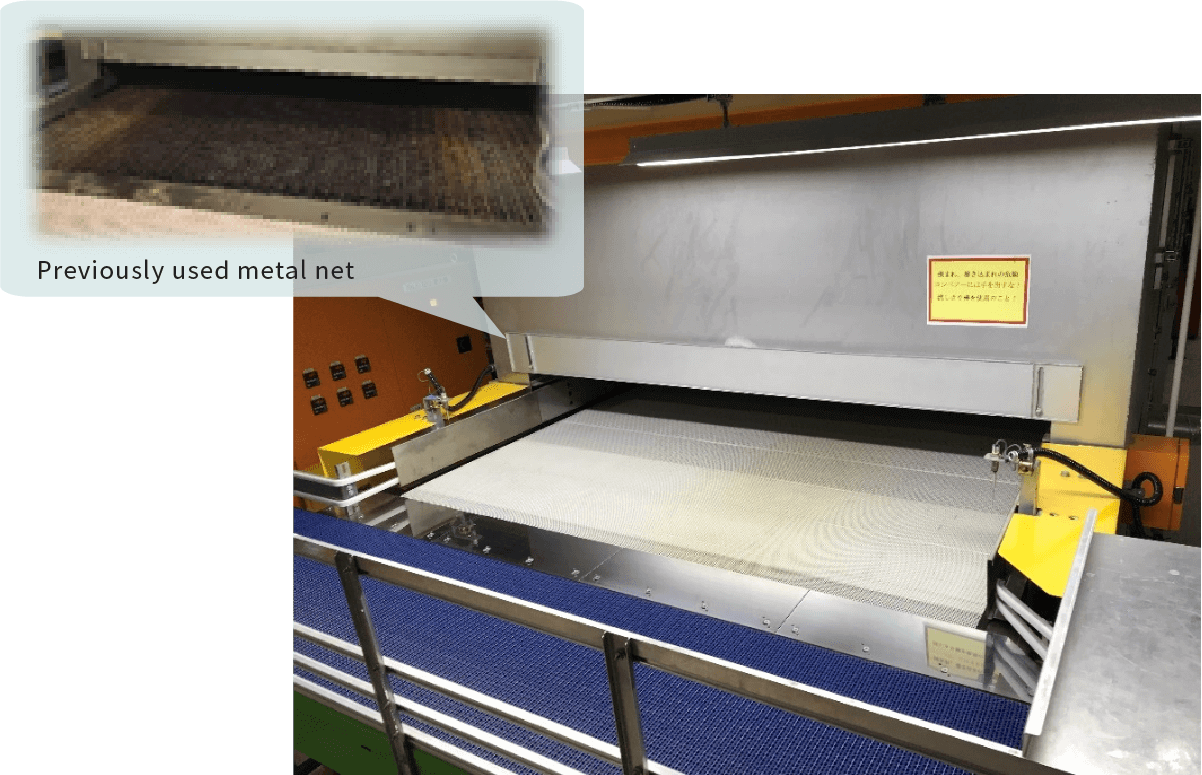

Renewable Energy Use
Onsite PPA Implementation
For implementation of renewable energy, we are now studying the introduction of onsite PPA* at our group's offices. We are planning to use all electricity generated by the solar equipment for our own operations. We also aim to achieve carbon neutrality by 2050 through expanded use of renewable energy through purchasing.
*Onsite PPA: Short for "Onsite Power Purchase Agreement". A system in which a power generation company (PPA company) is provided a space, such as the roof of a customer's building, to install power generation equipment on the site with the facilities that consume the electricity. The PPA company supplies the generated electricity to the customer and operates and maintains the power generation equipment.

Minimizing Scope 3 GHG Emissions
Minimizing GHG Emissions through Group Synergies
We aim to minimize Scope 3 GHG emissions by improving efficiency of receiving orders, production, and transportation throughout our group through consolidation of production for similar products and optimization of shipping systems based on the distance to delivery locations.

Promoting Lightweight and Recycled Materials
Minimizing GHG Emissions in Product LCAs※
The Altemira Group will contribute to minimizing GHG emissions throughout its product LCAs, mainly by reducing the weight of aluminum cans and bottles and increasing the use of recycled materials.
※ Life Cycle Assessment: A method to quantitatively assess the environmental impact of a product or service over its entire life cycle (resource extraction - raw material production - product production - distribution and consumption - disposal and recycling) or at specific stages.
Weight Reduction
We will contribute to minimization of GHG emissions in product LCAs by reducing the weight of aluminum cans and bottles and reducing the amount of raw materials used.
Weight Reduction Targets
Size | 2022 | 2030 |
---|---|---|
350ml aluminum cans | 6% cut | 22% cut |
410B aluminum bottles | 7% cut | 17% cut |
※Base year: 2013
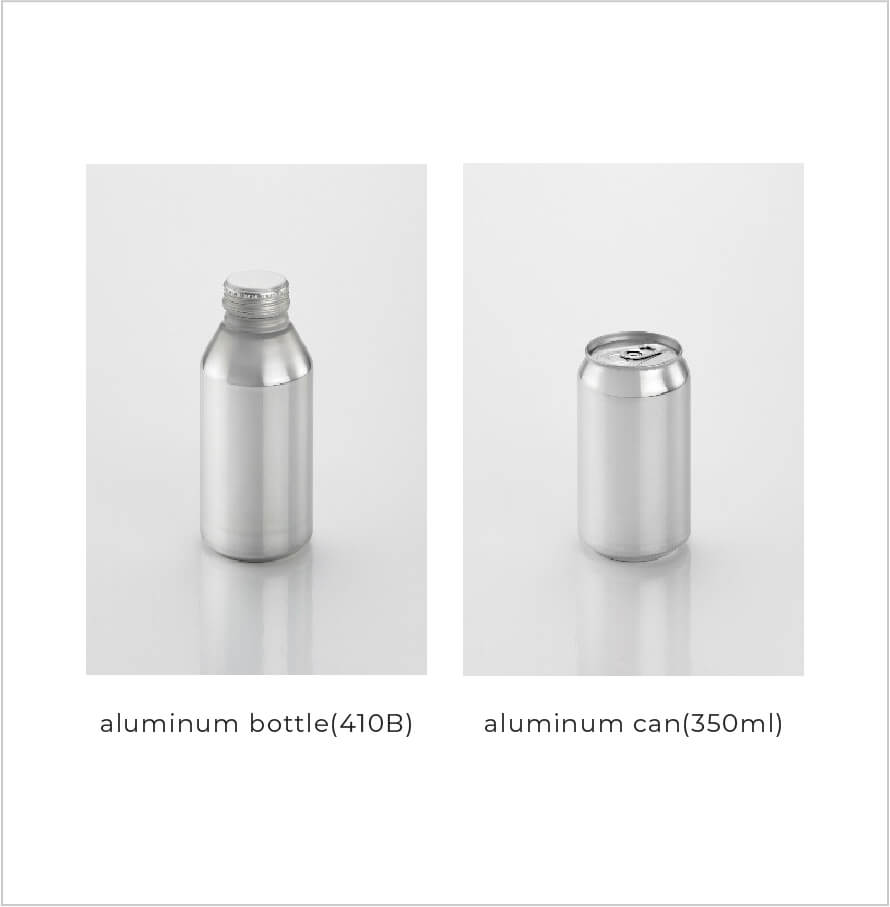
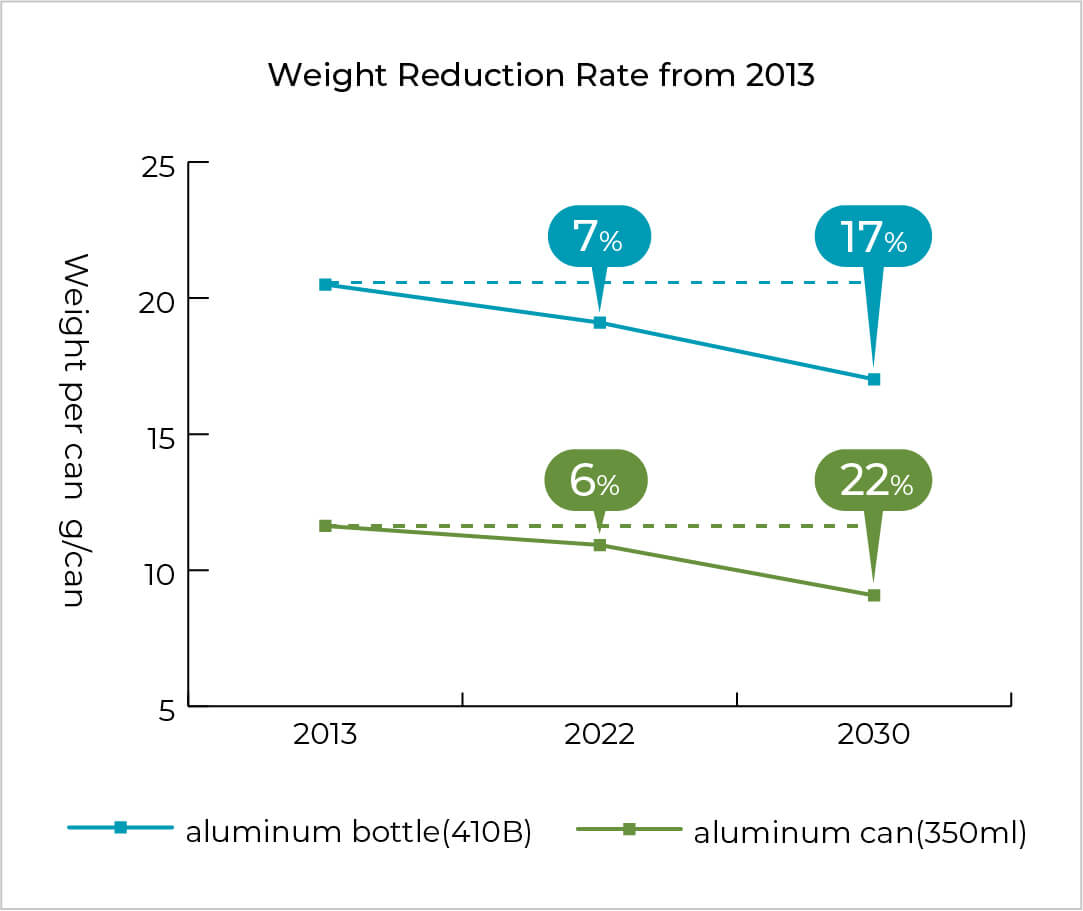
Expanding Use of Recycled Materials
In our aluminum can and bottle manufacturing, we have been proactively pursuing the use of recycled materials with lower GHG emissions, rather than new ingots with higher emissions. We will continue to promote the use of recycled materials and work to minimize Scope 3 GHG emissions in our product LCAs through technological innovations that expand the range of their uses.
See here for more information on recycling as a whole.